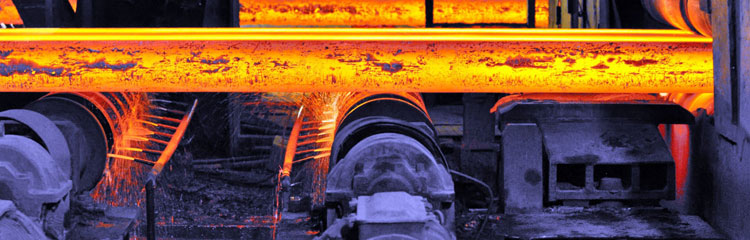
From scale pits to cooling water and wastewater treatment areas or final discharge ponds, there are various points where oil is bound to meet and mix with water.
From scale pits to cooling water and wastewater treatment areas or final discharge ponds, there are various points where oil is bound to meet and mix with water.
From scale pits to cooling water and wastewater treatment areas or final discharge ponds, there are various points where oil is bound to meet and mix with water throughout the steel production process.
Successfully removing and recovering oil from these various applications delivers significant benefits to those in the steel industry, including:
Common oil removal applications in the steel industry, include: