Turning Coolant Contamination into a Profitable Oil-Reclamation Program – Reprinted from Fluid & Lubricant Ideas
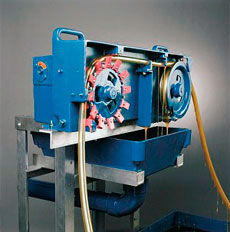
What started out as an expensive problem of metalworking coolant contamination has been turned into a profitable oil-reclamation program. Van Huffel Tube of Warren, OH – a manufacturer of welded tubing – was spending about $3,000 per year in recharging a soluble-oil coolant tank that would become contaminated with tramp lubricating oil. The 1,000 gallon tank had to be recharged about once a month with 100 gallons of soluble oil and 900 gallons of water.
The installation of a Model 6V oil skimmer not only eliminated the contamination problem – the soluble oil coolant tank has not been recharged in one year – but the reclaimed oil was sold for an annual profit of $5,500.
The skimmer, manufactured by Oil Skimmers Inc., operates 24 hours per day, five days per week, and 50 weeks per year. Payback of the installation cost was less than nine months as a result of the soluble oil saved and tramp oil reclaimed.
“We have operated the oil skimmer unit for over a year without one minute of downtime for maintenance. We are very happy with its performance and dependability,” says Ted November, plant engineer. “In addition, the skimmer is so efficient – the collected oil contains only about 5% water – that we get top dollar for the reclaimed oil.”
Oil-Laden Coolant Cleaned
Van Huffel forms flat sheet stock into welded tube in the Warren plant. Soluble oil is used as a coolant in the forming operation, where it picks up tramp oil from the sheet stock or from the forming equipment. The oil-laden coolant then goes to the 1,000 gallon collection tank where the tramp oil rises to the surface. If not quickly removed, the surface oil can coagulate and create a removal problem.
“We remove about 55 gallons of oil per week from the soluble oil,” comments November. “We collect it in two tanks, which feed a holding tank, and then sell it to a reclaimer.”
The free-floating, closed-loop collector tube used in the Model 6V oil skimmer is made of durable polyurethane, which attracts oil – not water. The tube adjusts to the coolant level and slowly moves over the surface, keeping the surface oil broken up. The collector tube is drawn up through the scrapers, which remove the tramp oil, and is then returned to the tank surface.
The system does not suffer from the clogging and parts-maintenance problems often encountered with other types of skimming systems because the collector tube works around any debris that may be floating on the coolant surface. External parts that do come in contact with the grit-laden oil are made of high-abrasion-resistant ceramic that resists corrosion. The collection tube is not only durable but also capable of withstanding temperatures of up to 200 degrees F.
The Model 6V skimmer has no tail pulleys or idler wheels to be hooked up below the surface of the coolant, thus installation is simplified, and inconvenient underwater maintenance is eliminated. Also, the skimming unit gear system has been designed to eliminate unnecessary strain when in use, creating only minimal power requirements.